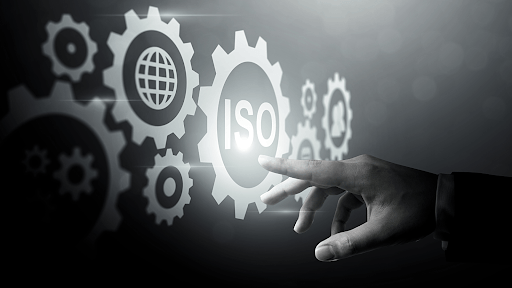
Blog Detail
The Ultimate Strategy to Enhance Operational Efficiency
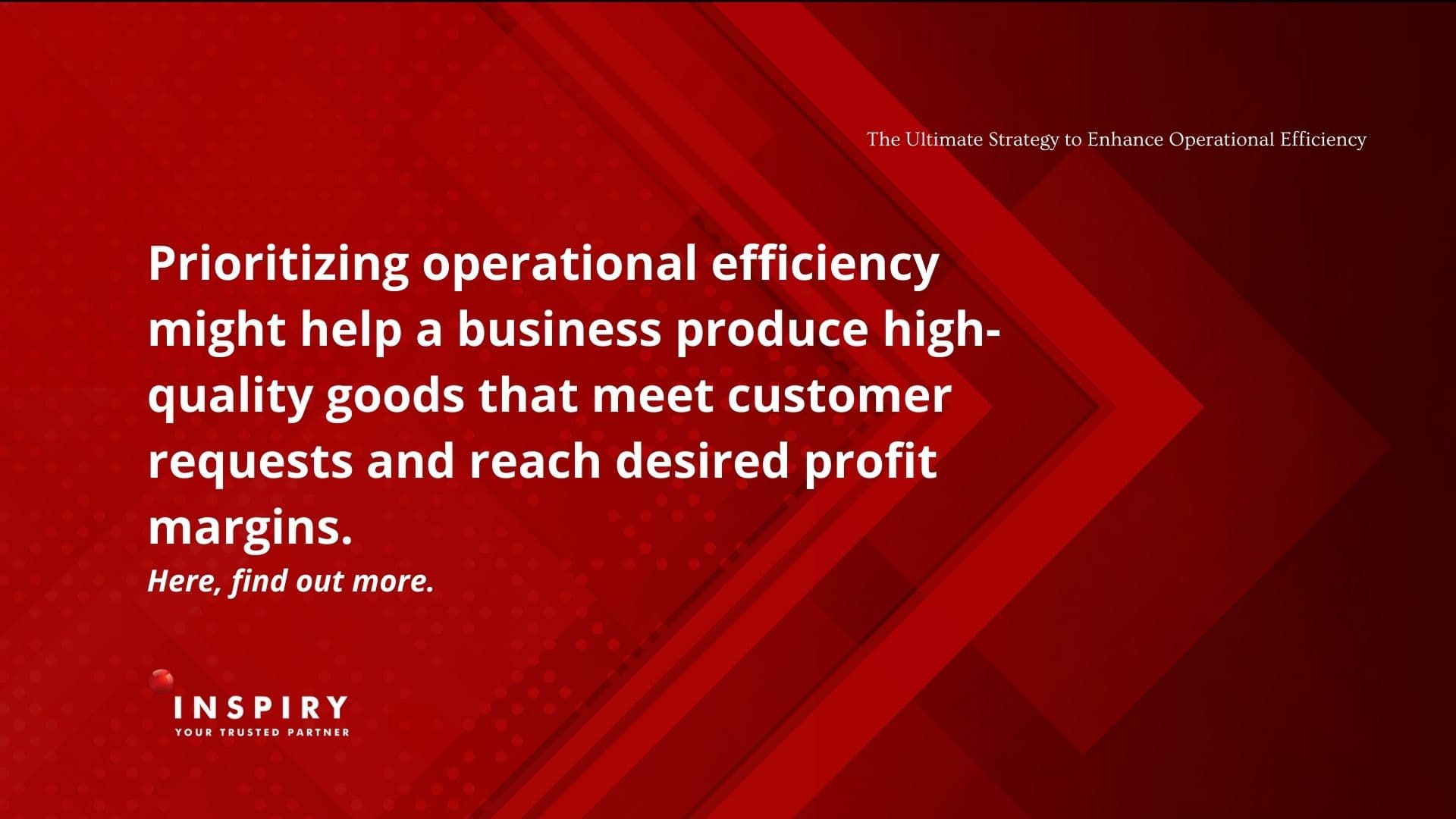
Business Operational efficiency refers to the capacity to utilize fewer resources while maintaining the same output level. Thus, lower costs that generate higher revenue have greater efficiency. Prioritizing operational efficiency might help a business produce high-quality goods that meet customer requests and reach desired profit margins. What is Input? Inputs are all activities and items related to the overall operational process, such as operational strategy, expenses, labor costs, and employee time. On the other hand, outputs include product or service quality, revenue, and client acquisition and retention. High operational efficiency businesses typically fulfill or exceed client expectations, establish a competitive edge, and enhance internal processes to handle rising demand.
Utilizing resources efficiently aims to cut down on waste in operations and manufacturing. Another strategy to boost output is by organizing and ensuring that your staff and the tools operated effectively. In distribution, handling final goods through effective routing and delivery can make a significant impact. In order to prevent expensive warehousing, inventory management aims to manufacture and manage inventory in a way that meets demand while not exceeding it. This emphasizes that the efficiency level is calculated from the utilized input and gained output. One of the theories to improve operational efficiency is Lean Six Sigma, which combines lean manufacturing and six sigma concepts.
Lean Manufacturing Concept originates from the Japanese automotive industry that attempts to reduce waste and eliminate tasks that provide little value to the production process. Removing unnecessary activities from the system shortens the time needed for production, improves product quality, and lowers overall costs. Five principles of lean manufacturing concepts:
Define value: Begin the lean approach by understanding the product value from a customer perspective, with the source of demographic information, interviews, and surveys.
Map Value Stream: The objective of this step is to identify all of the activities that contribute to the values of the client, as a point of reference. Unnecessary activities are those that do not benefit the end consumer. The two types of waste are non-value added but necessary and non-value & unnecessary. Non-value but necessary wastes should be lowered to the absolute minimum, while the non-value & unnecessary wastes should be eliminated. By reducing and eliminating waste, customers will receive what they desire, while at the same time reducing the cost of producing that product or service.
Create Flow: After identifying unnecessary processes, establish a smooth process without interruptions, delays, or bottlenecks.
Establish Pull System: One of the critical aspects of operation is inventory management. A pull-based system is a strategy to reduce inventory and work-in-progress (WIP) items while ensuring that the necessary supplies and data are accessible for a smooth workflow. With a pull-based system, products can be manufactured and delivered just in time, when they are needed, and in the required quantities.
Pursue Perfection: By completing the first four steps—identifying value, mapping the value stream, building flow, and implementing a pull system—waste will be avoided. Lean thinking and continuous process improvement become ingrained in the organizational culture as a result of the fifth phase, achieving perfection. Every employee should make an effort to deliver items that are ideal while taking the needs of the consumer into consideration.
On the Other Hand, Six Sigma is a collection of techniques and instruments for enhancing company operations and managing quality. In order to increase the consistency and accuracy of process outcomes, Six Sigma seeks to improve quality by identifying problems, identifying their causes, and upgrading procedures.
The approach of lean sigma is ‘DMAIC’:
Define: Define the goals and understand the process
Measure: Map the current process and collect the available data
Analyze: Identify the root cause
Improve: Implement and verify the solution
Control: Maintain the improvement.
The quality and timeliness of product delivery improve along with increased efficiency and fewer faults, which should also boost employee morale and confidence as well as the bottom line of the business.
Want to know more? Join our inspiring training program and increase your company’s operational efficiency!
Contact us via:
E-mail: inspiryindonesiakonsultan@gmail.com
Website: www.inspiryconsultant.com
Instagram: @inspiry.indonesia
Mobile: +62 877 6777 1778
Salam Inspirasi,
apt. Syifa Amirta Sani, S. Farm